総論 幅広く、奥の深い工作機械技術の面白さ
航空機産業にみる工作機械の変革
消え去る仲間と新たに出現した仲間
東京工業大学 名誉教授 伊東誼
図4 | 一体削り出しパネル部品-1990年代(AI合金製、サーブ社Elwingsonの好意による) |
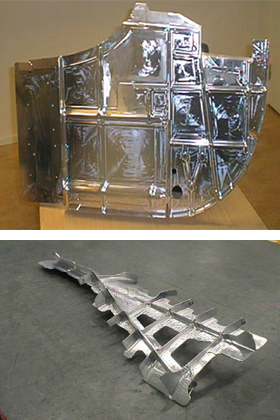
大きさ:約700×700mm、側壁厚さ:1?2mm、ウエップ厚さ:1mm
図5 | レール形CNCプロファイラー(Lシリーズ、シンシナティ・ミラクロン社、1990年代) |
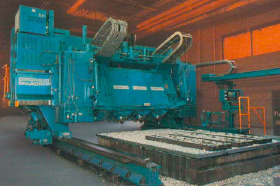
図6 | 航空機部品加工用ガントリー形MC-FZ100型、2014年(ツィンマーマン社による) |
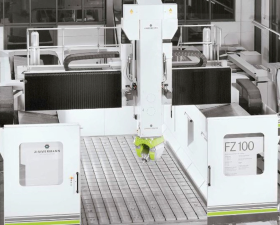
工作機械と飛行機に興味のある学生さんならば、航空機部品と聞けば、直ちに「一体削り出し」を思い浮かべるであろう。部品は素材からを不要な部分を削り去って創り出し、その際にはできる限り削り去る量を少なくするのが機械加工の鉄則である。
ところが、航空機部品では、素材のうち切屑として削り去る量が旅客機用で90?95%、又、軍用機用で95?98%にも達している。部品として使われる材料は実に1割にも満たないので、世間で喧伝されている「無駄の排除」とは完全に逆行しているが、何故であろうか。
航空機は空を飛ぶので軽く強い、いわゆる軽構造とせねばならず、更に高い信頼性が必要、不可欠である。そこで、「材料の疲れ限度に基づく設計」がなされていて、その大前提は疲れ限度の低下を招き易い、欠陥を内包しやすい素形材の使用を極力排除することにある。例えば、幾つかの小さな部品を溶接した部品は欠陥を持つ確率が高くなるので、無垢の素材から部品の一体削り出し加工を行うことになる。
「材料の疲れ限度」と聞くと、難しい話しと思われるであろうが、針金で垣根を修理している時に「ペンチ」がないので、針金を繰り返し折り曲げて切断した経験はおありだろう。これは、「針金が疲れ限度に達して壊れた」結果である。
要するに、乗客の安全を最優先にした上で、乗り心地が良く、速く飛ぶという航空機という製品の特質が加工技術に反映している。ちなみに、航空機部品ほどではないが、一体削り出しを行うのは、他に大形コンピュータの水冷用「マウントモジュール」があり、80%ほど除去する。これは、長い年月の間に残留応力が解放されて部品が変形して、水漏れが生じることを防ぐためである。
さて、「技術の質的な面」での工作機械の最大のユーザは、航空機産業と言われている。又、全ての部品加工に工作機械が直接的に関与すると言っても過言ではない。同じ乗り物でも、車体はプレス機で加工され、そこで使うプレス金型が工作機械で創り出されるように、自動車では工作機械は間接的に関与することが多い。
航空機部品は、大きくエンジン関係、並びに翼と機体関係に分けられる。軽量とするために、多少の例外はあるものの、すべての部品が「薄肉構造」で一体削り出しであり、しかも、部品が薄肉であるにもかかわらず、単位時間内に出来るだけ多くの不要な部分を削り取るという重切削が行われる。この様式の重切削では、加工中の部品に作用する加工力は小さいが、それでも部品が薄肉であるので変形しやすい。ちなみに、許される変形は1?10μmのオーダであり、又、加工中に好ましくない振動が生じやすいので、高度の加工技術が要求される。
エンジン関係の部品には、駆動軸、タービン翼、排気コーンなどがあり、いずれも削り難い耐熱合金やチタン合金、いわゆる難削材が素材である他に、チタン、あるいはアルミニウム・ハニカム構造材を使った部品もある図1。更に、2005年頃からTiAlの導入も進んでいる。これらの部品の多くは、他の産業でも使われている一般的な仲間(機種)、すなわちマシニングセンタ(MC)、立旋盤、クリープフィード研削盤などで加工されるが、仕様の一部を難削材加工向けに改良している他に、加工技術には高度のノウハウがある。
図1 | 戦闘機「トーネード」用タービン翼 |
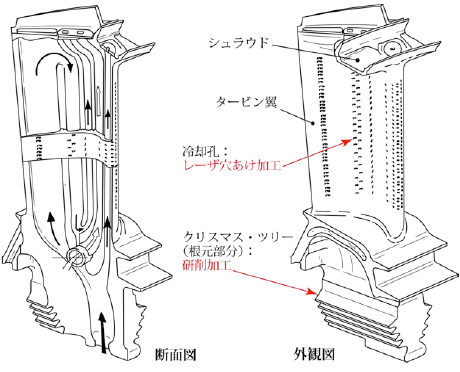
もちろん、素材は削り去る部分がなるべく少なくなるように、いわゆる「ニヤネットシェイプ(仕上り部品にできる限り近い形状・寸法)」となっている。しかし、大きな形状であると、ベーン部品のようにチタン合金を電子ビーム溶接して素材を準備している。又、あまりにも複雑な形状のエンジン部品、例えば直径1,600mmで壁厚約20mmのエクゾースト・ケースは、安全性や信頼性を十分に吟味した上で、削り取る量を最小化した溶接素材となっている図2。
注意すべきは、エンジン部品の場合には、工作機械単独ではなく、例えばタービン翼の固定治具も含めてシステム、すなわちフレキシブル・加工セル(FMC)として論じられることが多い。これは、難削材を高精度、しかも信頼性の高い部品に仕上げるために、素材の作り方から前加工、主加工、並びに後加工迄を一貫して考えねばならない必要性が航空機部品の場合には特に大きいためであろう。又、軍用機のエンジンの場合には、部品を加工後に必ず全数検査を行なうために、システムに三次元測定機を組入れている図2。
図2 | エクゾースト・ケース加工用FMC-“PW4000“、1986年(コングスベルグ社による) |

ここで、商売の上でも技術の面でも興味あるエピソードをひとつ。1980年代後半には、ノルウェー、コングスベルグ社が世界中の民間機及び軍用機の殆どすべてのタービン翼を生産していた図3。
図3 | タービン翼研削加工用FMC-“RAMIGO“(コングスベルグ社) |
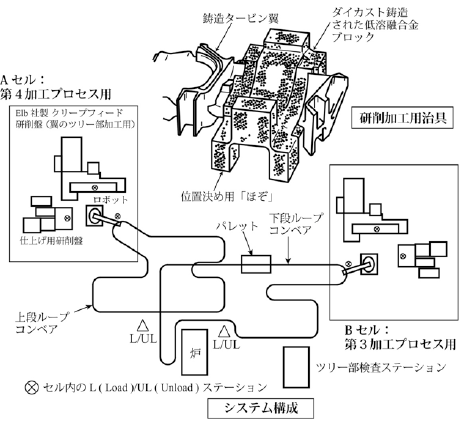
この頃に、東芝機械のココム違反事件、すなわちソ連の原子力潜水艦用プロペラ加工機をレニングラード工廠へ輸出した事件が起きた。実は、この機械の数値制御(NC)装置はコングスベルグ社が別途ソ連へ納品していたので、米国から強い抗議が同社にあった。あまり執拗であったので、最後に「それならば今後は一切米国の軍用機のタービン翼は作らない」と回答したら、米国の抗議は沙汰やみになった。要するに、死命を制するような製品を独占して生産している企業の強みを示している。もっとも、その後には米国は自国内でのタービン翼生産設備を整備したと言う後日談もある。
さて、エンジンと対照的であるのが翼や胴体の部品を加工するプロファイラー(スキンミラー)及び桁フライス盤である。実は、一体削り出し加工と特徴づけられるのは、翼と胴体の部品に多く図4、又、プロファイラーも桁フライス盤も、単位時間当たりの切屑生成量が大きいと言う意味での重切削能力を備えていて、それは高速主軸と同時に大馬力の主電動機で実現している。例えば、シンシナティ・ミラクロン社製CNCプロファイラー(Lシリーズ)では、最高主軸回転数10,000rev/minで主電動機出力は100HPである。ちなみに、一昔前にはシンシナティ社のプロファイラーが飛行機部品の加工工場の顔であり、その設備台数で飛行機の月産能力を正しく推測可能と言われた。もちろん、シンシナティ社のドル箱であった図5。
ところで、航空機の進歩に伴って加工技術や素材などの改良が進み、航空機用工作機械で現在大きな変革が起きている。実は、プロファイラーや桁フライス盤は5軸制御MCやガントリー形MCに代替されている図6。又、翼の中を貫通しているAl合金製の桁や表面のパネル部品を強くて軽い炭素繊維複合材(CFRP)で作り、削り出し加工を不必要とすることも行われている。このような無駄の排除を目指す技術開発は軍用機では積極的に行われていて、チタン合金製の戦闘機の風防を溶接素材から仕上げる試みもなされている。又、2013年には、3Dプリンター製ロケットエンジン部品(推力約9tonf)の試作研究もNASAで行われたと報じられている(Gent 2013)。しかし、軍用機では許される冒険的な試みを旅客機に適用するのはまだ先の話であろう。ちなみに、戦闘機は20年位先を読んで当初の設計構想を練るのが普通である。
要するに、航空機部品の加工に長く用いられてきた象徴的な仲間が、一般的なMCに置き換えられつつある。そして、それが新素材の採用で加速されている。となると、新たな仲間が必要になるのではないかと思われるであろう。もちろん、その通りであり、例えばCFRPは加工の難しい材料であることに加えて、CFRPを異なった材料と重ね合わせた部分の穴あけは、基本的にドリルが曲がり易く難しい作業である。
そこで、ドリルの刃先を改良したり、遊星方式穴あけでバックアップ材を用いたりしている。しかし、これら従来の方法では垂直方向に作用する切削抵抗によって、複合材の最上部の積層材がしばしば損傷する。色々な加工方法の改良の中で注目されるのは、カールスルーエ工科大学により提案された、Taumelfrasen(英語名はWobble milling)と称するFRPの穴あけ方法である(図7、Schulze & Becke 2009)。この方法では、公転軸に傾斜して設置された工具軸が自転、すなわち歳差運動をしながら工作物厚さの中心部に向かって穴明けを行い、これにより積層材の損傷を防止する。
航空機の加工技術の場合には、民間機と軍用機の間に明確な区別はなく、正に「灰色」である。その結果、軍事機密となっているところが多く、最先端での工作機械の変革は今一つみえないこともある。
図7 | Wobble Millingの概念(SchulzeとBeckeによる、2009年) |
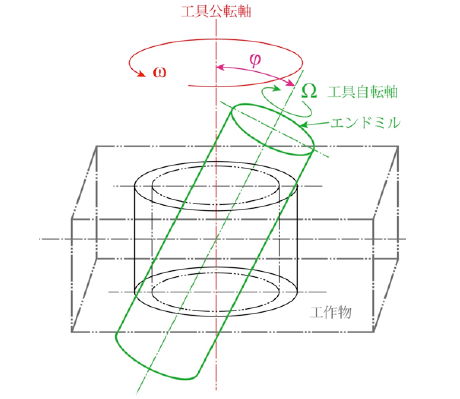
参考文献
Gent E. (28 Aug. 2013). Nasa tests largest ever 3D-printed rocket component. E & T Magazine, IET.Schulze V, Becke C. (2009). Taumelfrasen zur schadigungsarmen Bohrbearbeitung von Kompositwerkstoffen. ZwF; 104-6: 473-477.