5軸制御立形マシニングセンタ DA500の開発
切削と旋削、
二刀流でも一流を目指す。
歴史と意地と誇りをかけて
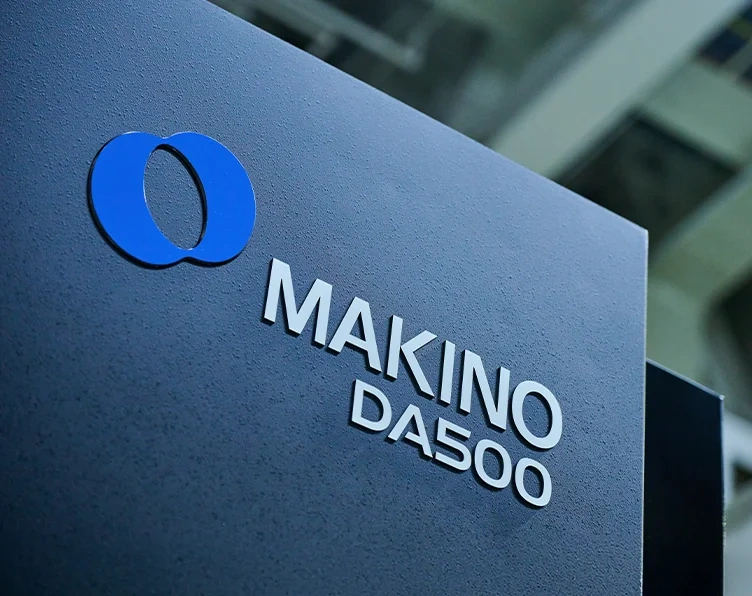
マキノが部品加工に特化した5軸制御立形マシニングセンタ
「DA300」を発売したのが2016年7月のこと。
それまでのマキノの立形マシニングセンタは部品加工よりも金型加工が得意というイメージが強かったが、これをきっかけに評価が変わり、新たな国や業界での導入が広がった。
それから約7年後の2023年10月、今度はさらに大きなワーク(工作物)を加工でき、しかも切削加工だけでなく旋削加工も付加できる「DA500」を発売した。
創業以来、切削加工に注力してきたマキノが、実績の少ない旋削加工にあえて挑戦したのはなぜか。
他にもGIブレーカや、ユーザーの作業ミスを減らす新しいビジョンシステムなど様々な機能を搭載した「DA500」はどうやって生まれたのか。
これまでなかったものを世に生み出すことの難しさと歓び、そしてマキノならではの意地と誇りをかけた開発の日々を紹介する。
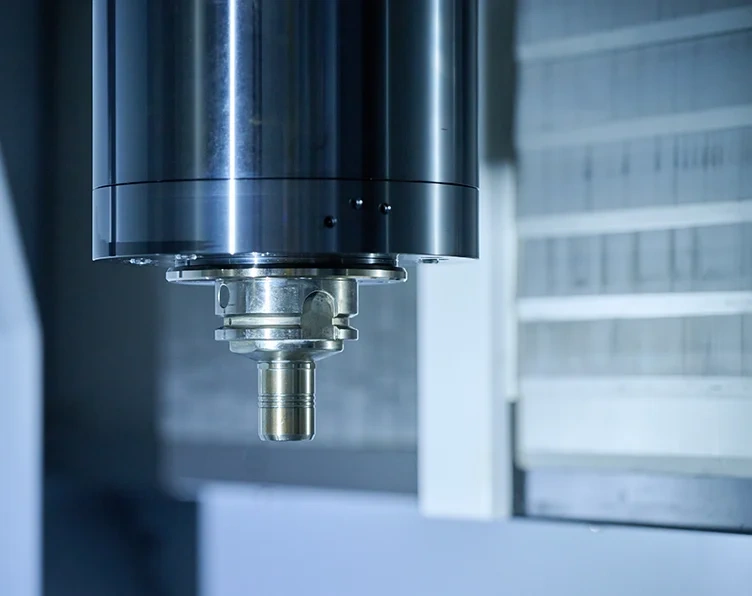
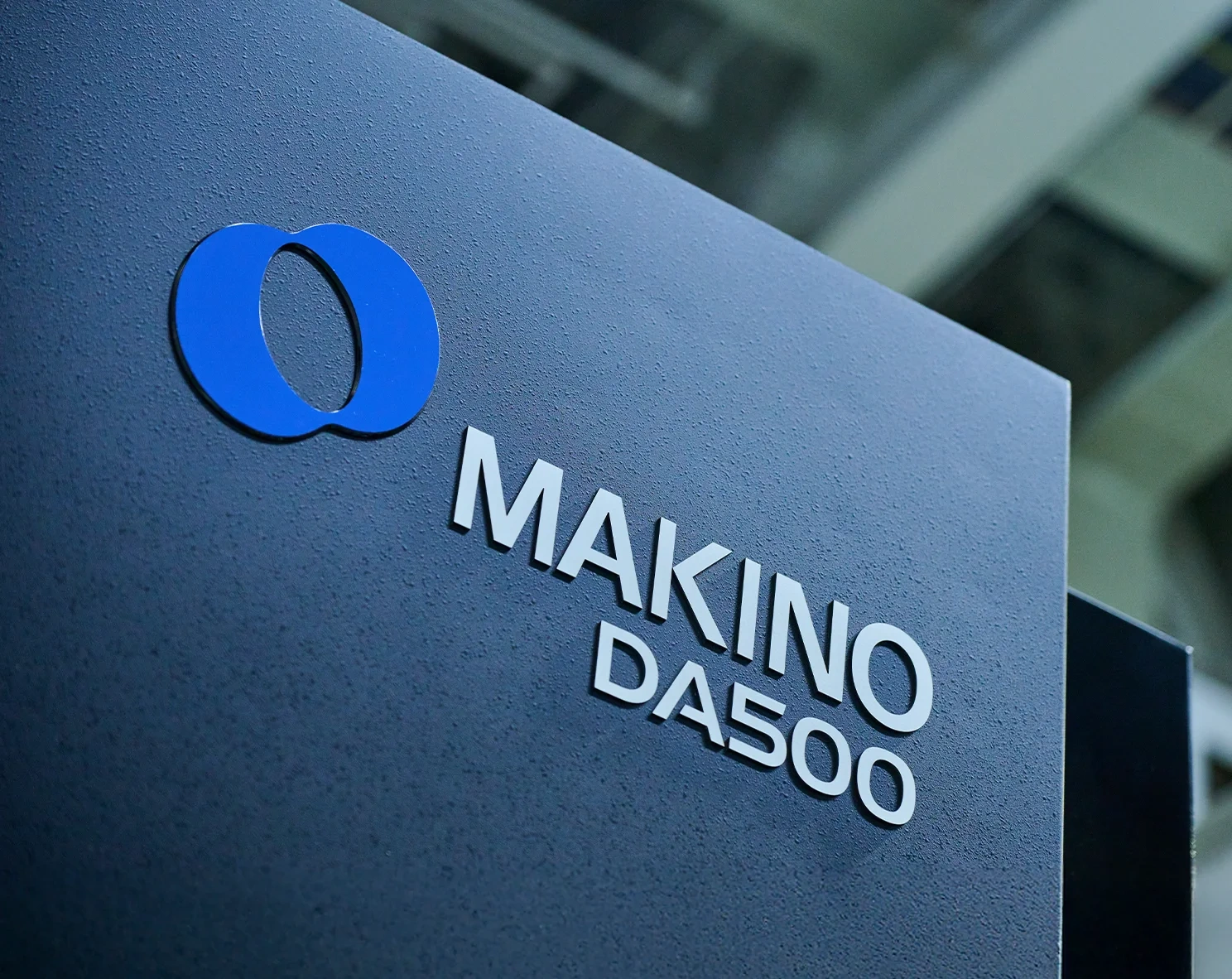
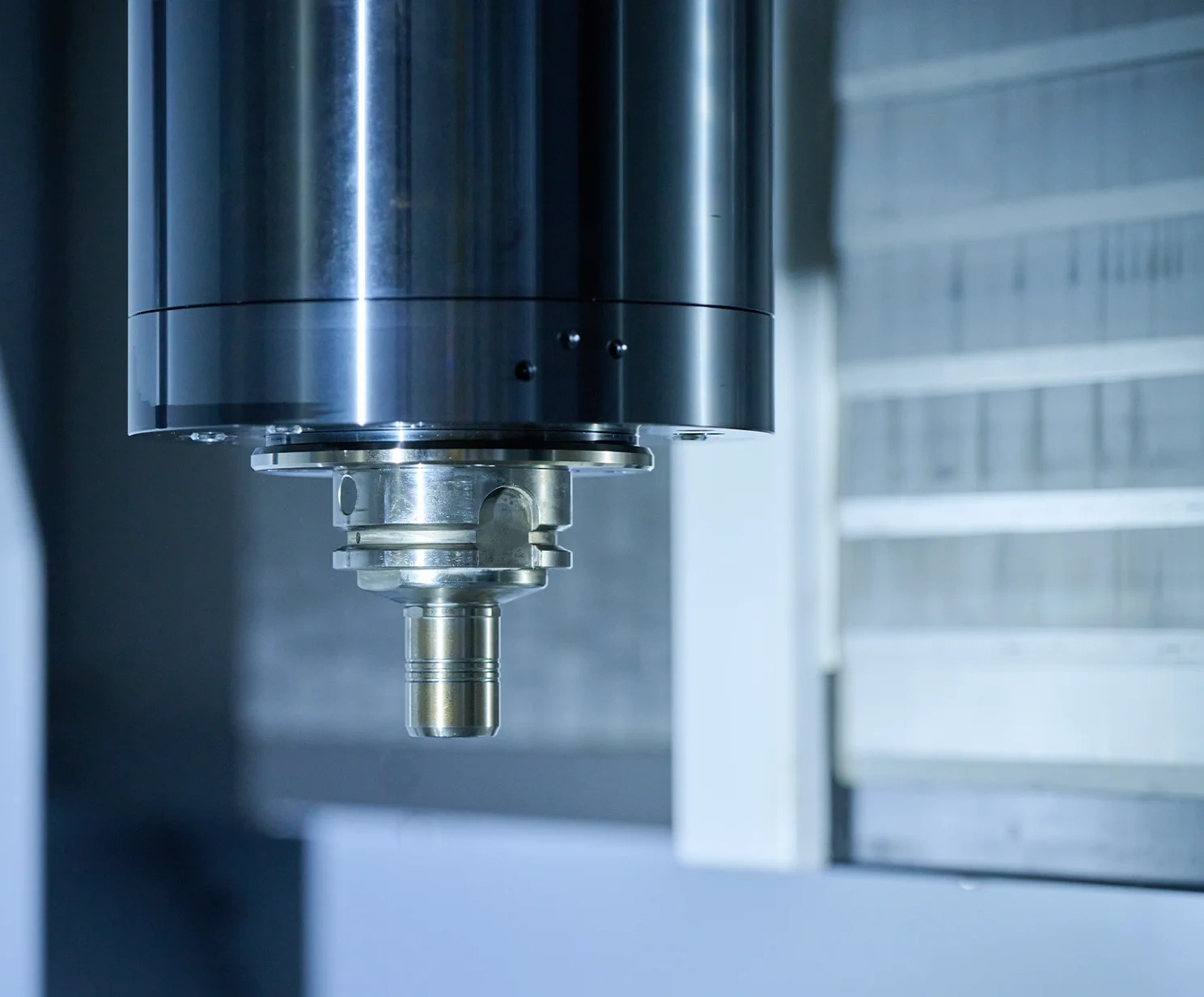
MEMBER
メンバー
-
寺川 慎二SHINJI TERAKAWA
開発本部 商品開発部1 DAグループ / 2004年度新卒入社 / 工学研究科機械工学出身
DA500のプロジェクトマネージャー。歴代の新機種開発に数多く携わってきた。座右の銘は「一生懸命だと知恵が出る、中途半端だと愚痴が出る、いい加減だと言い訳が出る(武田信玄)」
-
工藤 真也SHINYA KUDO
開発本部 機械制御開発部 / 2010年度新卒入社 / 理工学研究科・知能機械システム工学出身
制御ハード担当として、制御回路の設計、部品選定、制御盤筐体の設計に携わる。この開発要請で別事業所からメンバーに加わり現在に至る。「忘年会で皆と飲んだビールが最高でした!」
-
古田 恵MEGUMI FURUTA
開発本部 機械制御開発部 / 2010年度新卒入社 / 情報工学科出身
DA500では、作業者の段取りミスを減らすための新機能Vision W.S.C.(特許出願中)の開発を担当。夫と家事・育児を分担し、短時間勤務も活用しながら仕事との両立を図っている。
-
石丸 謙造KENZO ISHIMARU
開発本部 基盤技術開発部 基盤技術グループ / 2014年度新卒入社 / 量子理工学出身
主軸開発の専門チームに所属。DA500の要、マキノでは初となる切削専用機と旋削加工機の両方に対応した新機構を持つ主軸を開発した。現在もこの技術を応用した次世代主軸の研究・企画・開発を進めている。
-
樋口 裕太郎YUTARO HIGUCHI
開発本部 機械制御開発部 / 2014年度新卒入社 / 工学部機械工学科出身
入社4年目にアメリカにある子会社のMakino Inc.に2年駐在。帰任後、切りくず分断機能のGIブレーカ(弊社特許取得)の開発に携わる。社内外で注目され、GIブレーカ開発チームとして社内の功績善行賞を受賞。
-
矢口 翔TSUBASA YAGUCHI
開発本部 商品開発部1 / 2018年度新卒入社 / 工学部機械工学出身
社内にない新技術の研究開発を行っていた流れから、DA500用に高速回転する旋削テーブルの開発を担当。1分間に800回転という目標値を達成。現在も旋削テーブルの開発を行っている。
用語解説
-
切削加工とは工具を使って金属などの材料を削る加工方法の総称だが、マキノではフライス加工(材料を固定し、工具を回転させて削る加工)をさし、旋削加工(固定した工具に材料を回転させて削る加工)と区別して用いている。
-
工具を自動で取り替えて様々な加工を連続で行える工作機械のことで、機械の構成によって、横形、立形、門形などがある。
-
通常のマシニングセンタの主軸やテーブルがX、Y、Zの直線3軸方向へ動くのに対して、そこに回転と傾斜の2軸を加えた5軸を同時に制御しながら加工する工作機械のこと。3軸のマシニングセンタでは、人の手を借りる段取りが必要な複雑な加工もすべて自動で行えるため、精度面、生産性、安全性などのメリットがある。
お客様が機械に求める声から見えてきた
マキノが目指すべき新境地
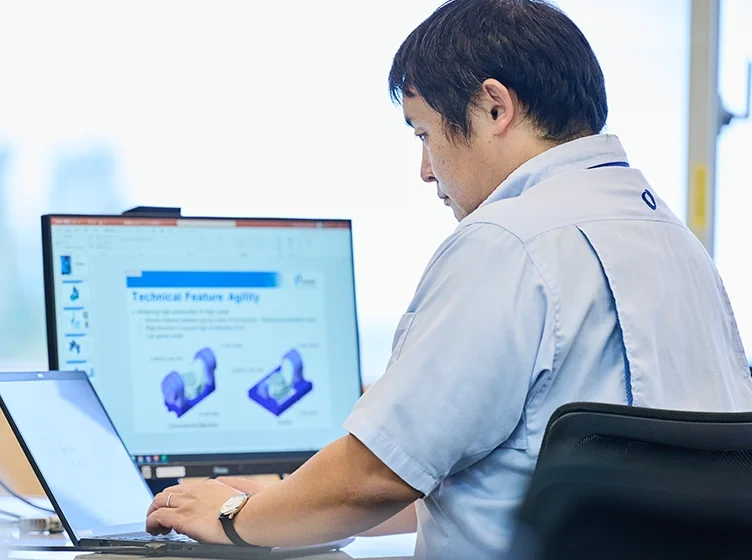
はじまりは開発本部長による海外視察。マキノがアプローチできていない領域が見えてきたことだった。「これまでのマキノの5軸機は、一台で金型加工も部品加工も幅広く対応するといったスタイルでした。でも、光学・電子部品、医療用製品など、部品加工に求められる技術がより複雑化する中で、従来のままでは部品加工の生産性に対するニーズに応えきれていないという現状に突き当たり、部品加工における精度も生産性もとことん追求するDAシリーズを開発しようということになったのです」。そう語るのは「DA500」のプロジェクトマネージャーとして技術者たちを束ねた寺川だ。「最初にDA300を開発する時点でさらに大きなサイズも加工できるDA500の開発も予定されていました」
構想としては、部品加工に特化したDAシリーズとしてまず「DA300」を発売。販売実績を重ねて、そこでの市場ニーズも取り込み、「DA500」の開発をスタートさせるという流れだった。そして計画どおり「DA300」は2016年7月に発売、「DA500」の開発は間を空けて2022年7月のスタートとなった。
寺川は自身も開発に携わっていた「DA300」の発売後、今度は「DA500」がメインターゲットとする半導体製造装置部品、航空宇宙、産業用ロボット分野でのリサーチを開始した。「自社の営業やCAC(カスタマアプリケーションセンタ)のメンバーとともに実際に何社かお客様を訪問し、機械に求める性能や機能について聞き取りを行いました。その中で、特にある分野の部品は加工面に旋削加工の指定があるケースが多いことがわかってきました」。以前は工程を分けて2台の機械で対応していた加工を、工程集約、効率化、精度向上、省エネ化などの観点から1台で行える工作機械がほしいというお客様の声、つまり切削と旋削ができる複合機能を有する5軸機の需要が高まっていたのだ。「これで、DA500には旋削加工機能を付けるべきという構想がまず固まりました」
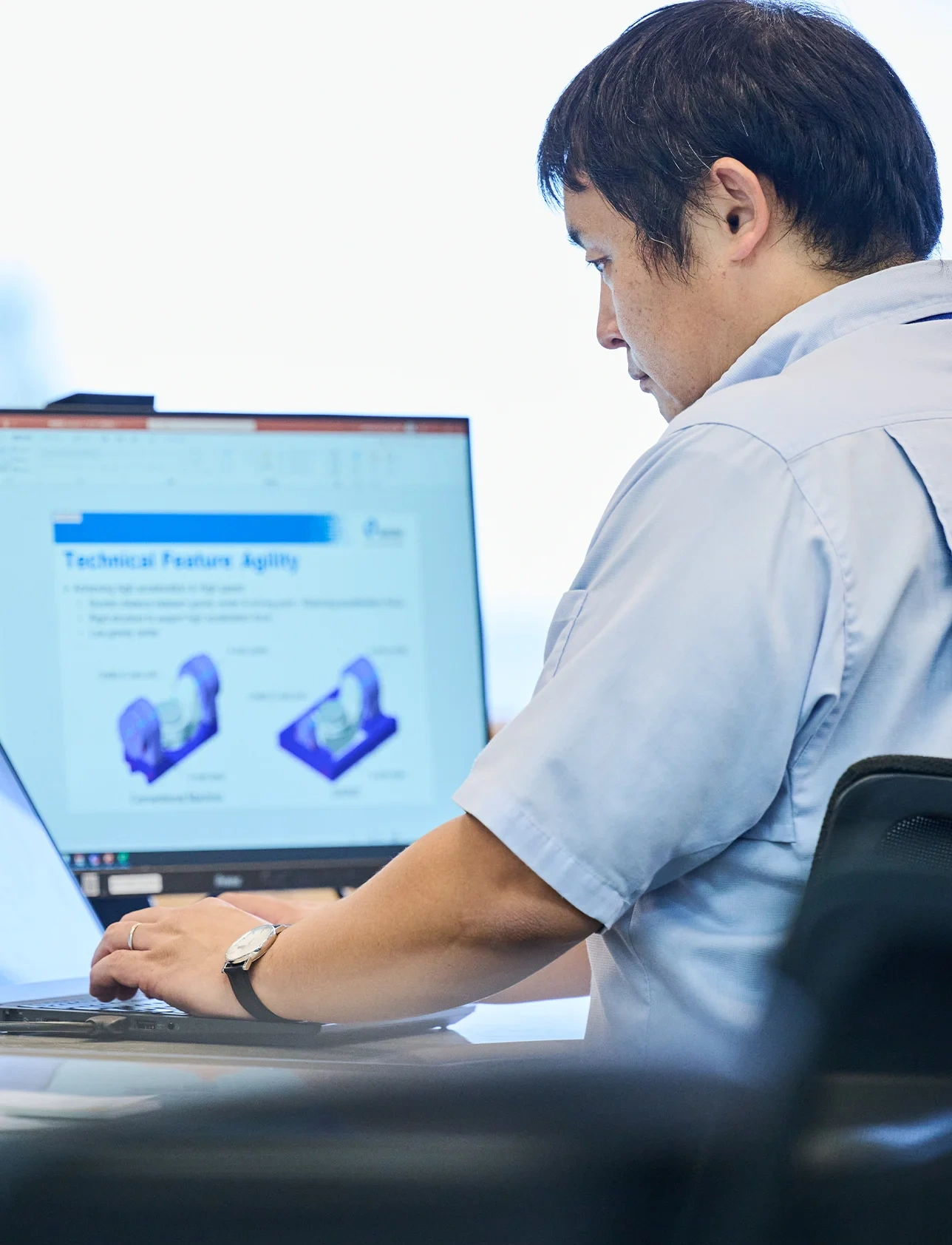
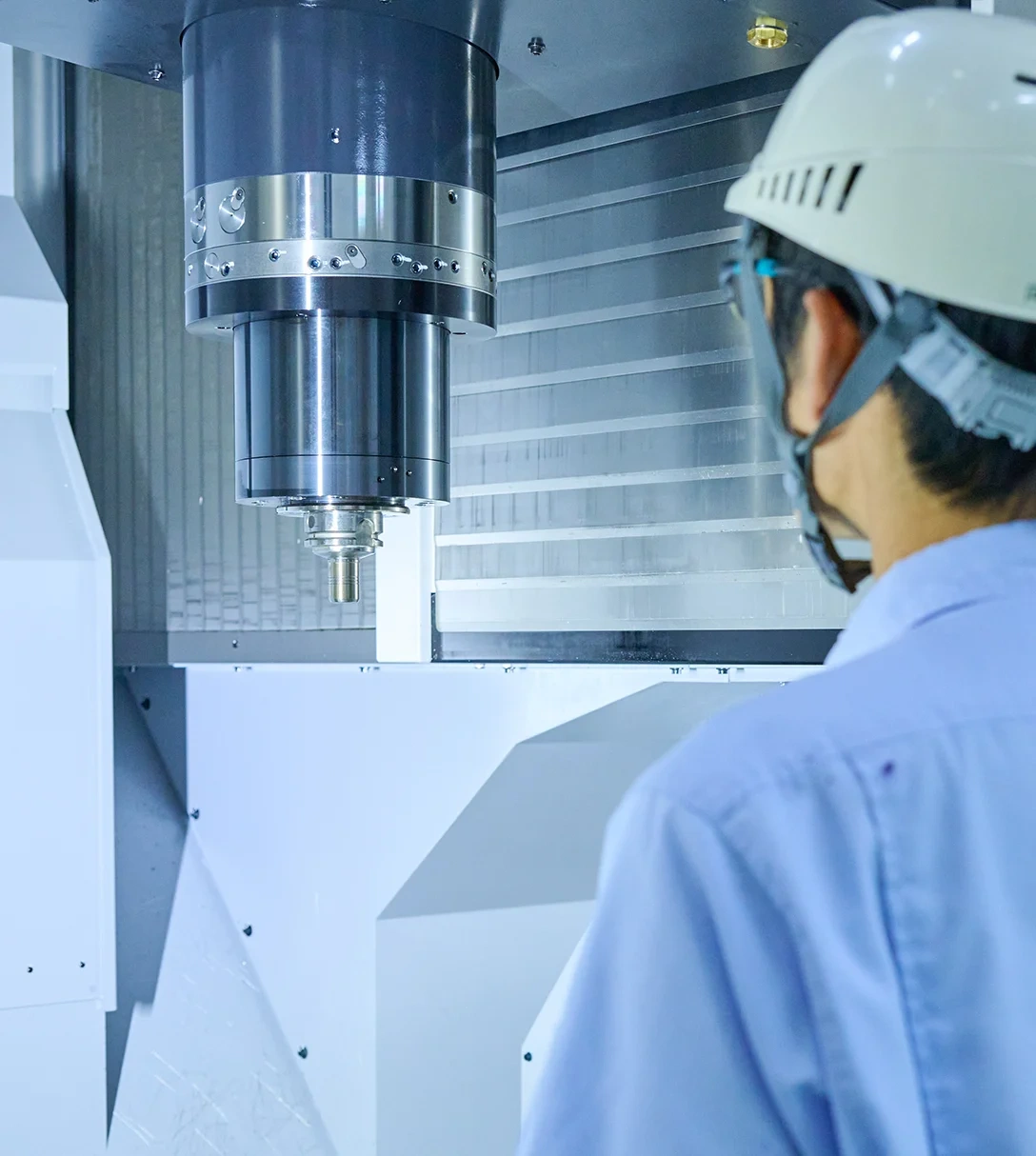
切削加工も旋削加工も高精度。
マキノにしかできない新しい主軸の開発
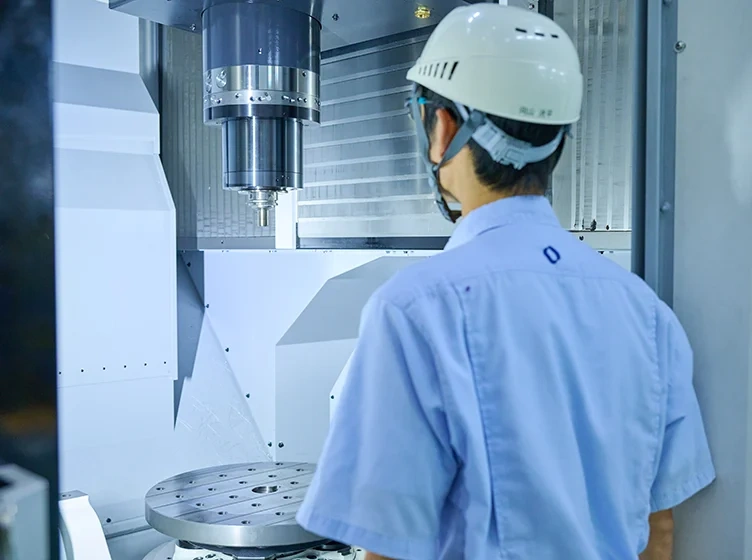
創業以来、切削加工にこだわり続け、社名にも回転切削工具を意味する「フライス」を掲げているマキノ。旋削加工に対する知見がほとんどない中で、加工の要となる主軸の開発がスタートした。主軸開発メンバーのひとりである石丸は当時どんな想いだったのか。「このプロジェクトが立ち上がる以前から私のいる主軸開発チームでは、旋削機能付きマシニングセンタの需要を見据えて新しい主軸の基礎研究を行っていました。DA500に旋削機能を搭載すると聞いたときは『やっと研究成果を世に出せる!』とうれしかったですね。でも『実験ではうまくいっても、製品に組み込まれたときにどうなるか』という不安もありました」と石丸は答える。
まず取りかかったのは、旋削加工時に主軸工具の回転を抑えるロック機構の開発だ。この旋削用主軸のロック機構はすでにさまざまなメーカーで実用化されていたが、その多くは旋削加工ができる代わりに切削加工の性能が下がるという犠牲を払っていた。「マキノの主軸は常に最高の切削加工性能を発揮できることを目指して開発されてきました。そのこだわりは旋削加工を付加するDA500の主軸であっても変わりません。他社の真似では実現できない、切削と旋削の2つの加工性能を両立した独自構造を開発する必要がありました」
従来の主軸構造にとらわれず、デザインのすべてを一から見直すこと。石丸は主軸開発チーム内で何度も意見を出し合い、強力なロック機構を内蔵したまったく新しい主軸デザインを考案した。これまでの主軸と構造が大きく異なるため、機械加工、組立、生産技術、調達部門など、各製造部門にも協力を仰ぎ、議論と製造プロセスの検証、設計改良を重ねた末での開発だった。「『これはできない』と何度言われたか。1回実験機をつくるだけなら『そこをなんとか頑張ってください』と押せますが、製品化するとなると、いままでと同じように作りやすく、高性能を維持できる仕様にしなければならないということで、本当にいろいろな部署に多大な協力をいただいて、なんとか完走できたという感じです」と表情をゆるめる。
次は誰が工程を止めるか。
もがきつつ、楽しくもあった未知への挑戦
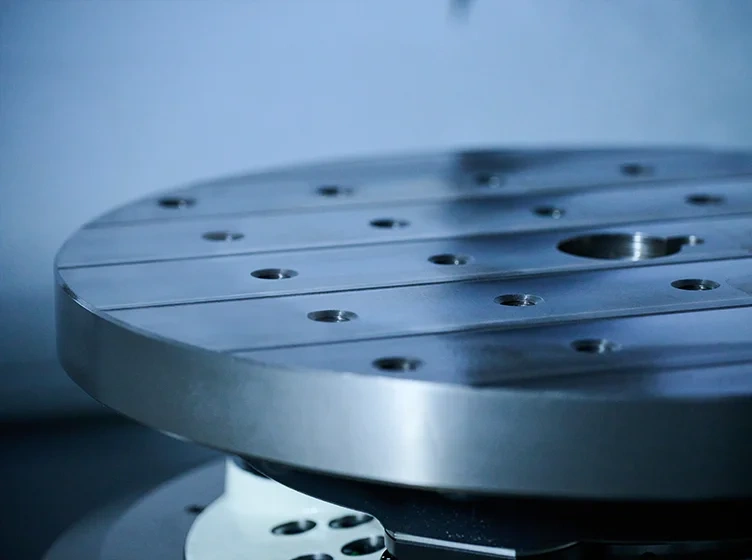
旋削機能を付加するためのもうひとつの要が工作物を載せて回転させる旋削テーブルの開発だ。これも主軸同様、「DA500」のプロジェクトに先行して検証を行っていた要素のひとつで、担当したのは20代の矢口。「自分自身テーブル関係の業務ははじめてで、しかもマキノ内部でもノウハウの少ない旋削テーブルということでまさに手探りでした。同じようなテーブルサイズは1分間に100 回転、今回の目標値は800回転。8倍もの高速回転を実現させるにはどうしたらいいか、上司や先輩だけでなく、生産部門、CAC、開発部門など、関連する部署の方々に相談しまくりました(笑)。ようやくテストする段階になっても、まず動かない。軌道修正してやっと動いたと思ったら別のトラブルが起こる。また助けを借りて修正する。その繰り返しでした。無事、800回転させることができたときは、わが子の頑張りを見ているようで幸せな気持ちになりました」とはにかんだ。

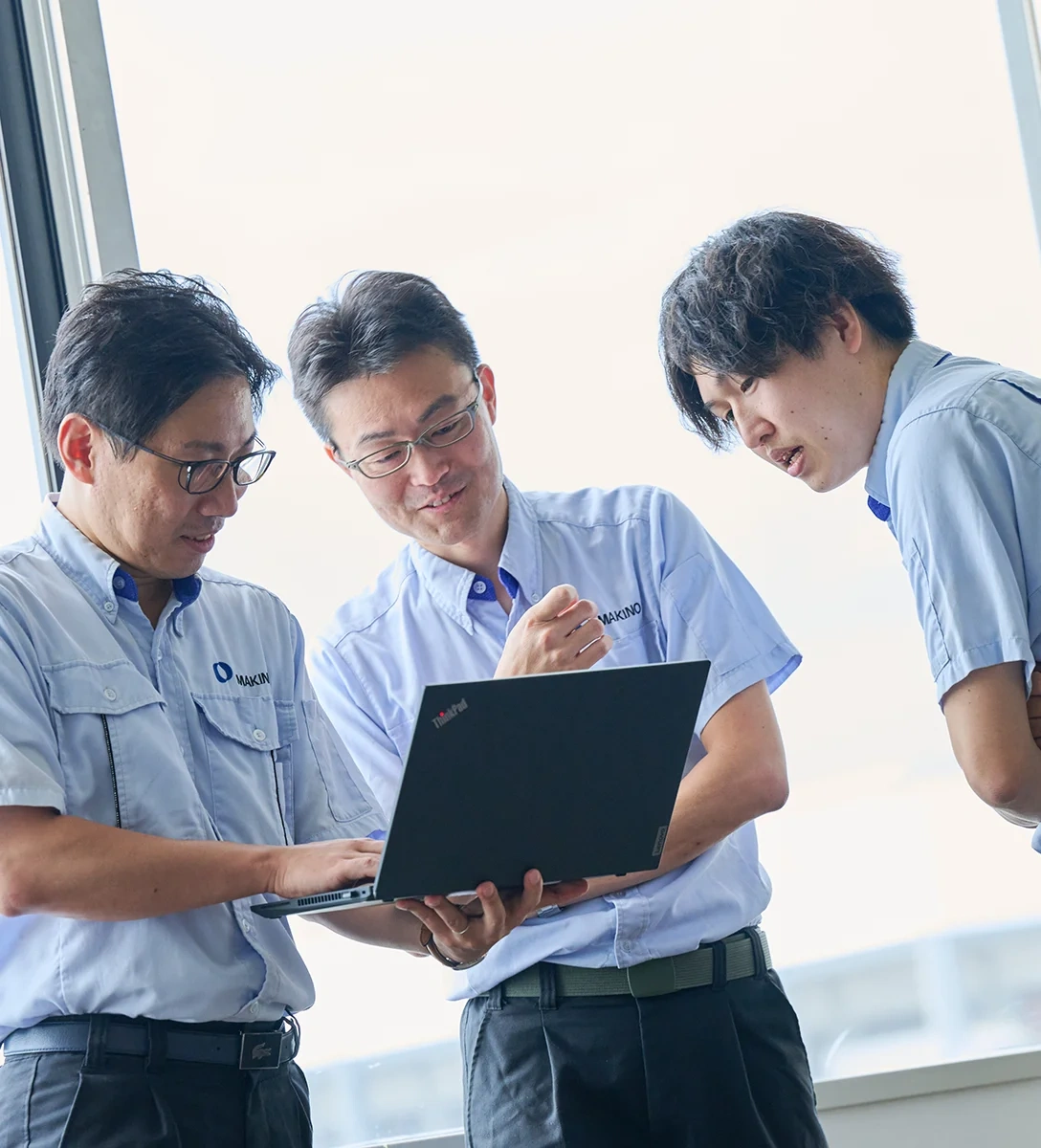
このプロジェクトの制御ハード担当として参画した工藤が言葉をつなぐ。「新機種開発ということで、各自それぞれに課題・難題を抱えていて『次に工程を止めるのは誰だ?』なんて言いながら、互いを励まし合って進めていましたね。自分も最初、びっくりするくらい機械が立ち上がらず焦りました。機械を動かすサーボ部分を、今回自分なりに厳選して新しい製品群に一新してみたのですが、それが故にどれが原因かわからず、1つ1つ部品を替えながら改善していきました。ハードウェアの問題もあれば、ソフトウェアとのミスマッチで複合的に発生している問題もあり、互いに協力しながら解決していきました。製造部門の方々には本当に申し訳なかったです。でも、ものづくりのエキスパートとして同じ方向を向いていることを肌で感じ、勇気をもらっていました」。以前から制御盤設計を共通化する取り組みを進めていたという工藤は、そうした他部署の協力もあり、共通化第1号の制御盤をDA500に実装することができた。
そして「DA500」よりひと足早く発売し評判となった新機能「GIブレーカ」の開発に携わった樋口は「GIブレーカが対応しているマシニングセンタへの標準仕様化が決まり、DA500にもGIブレーカを搭載することになってうれしかったですね。DA500の機械特性に合わせて調整を行ったのですが、皆さんの熱量に触れて、自分も開発当時のことを思い出しました」と続ける。「GIブレーカ」は穴あけ加工の新機能で、お客様のお困りごとの上位に位置していた穴あけ加工時の長い切りくずを送り軸の若干の脈動により細かく分断し、工具への絡みつきを防ぐというもの。マキノの強みである加工技術と制御技術(GI技術)によって実現することができた機能で、樋口は制御開発を担当した。「機械言語に関しては一からの勉強で、プログラムのバグや、機械を思うように制御できなかったり、切りくずが分断されなかったりと格闘していました。何度もトライアンドエラーを繰り返し、実現できたときは感無量でした」と当時を振り返る。皆、それぞれに悪戦苦闘しながらも、今までになかったものを創り出す歓びを感じていたことが伺える。そこに共通するのは、“ものづくりが好き”という想いだ。
展示会への出展が急きょ決定。
期待に応えるべく、各自ラストスパート
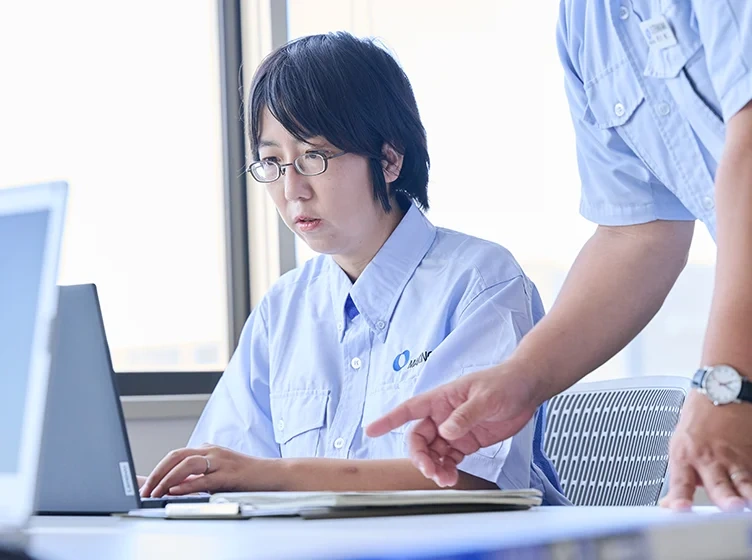
「私がプロジェクトに参画したのは、皆よりも少し遅い2023年3月です。開発中のDA500のための新技術として、WSS(段取りステーション)のマガジン内にカメラを付けて正しいサイズのワーク(工作物)が設置されているかをチェックする機能をつくってほしいとのことでした。しかも10月の展示会に間に合わせたいと。今まで携わってきた機能開発は年単位でしたので、残り半年しかないタイミングにとてもびっくりしました」。そう語るのは、今回「Vision W.S.C(ワークサイズチェッカー)」というビジョンシステムのソフトウェア開発とカメラ選定に従事した古田だ。
「古田さんが所属するチームに急きょお願いすることになったのは、DA500のために開発したパレットマガジンが大小さまざまなワークを載せることができる特殊な仕様となったため、お客様のミスを防ぐための新たなシステムが必要になったからでした。展示会はちょうどそのころに出た話で、私も寝耳に水でした(笑)。当然どこかの展示会に出すとは思っていたのですが、当初の発売目標が2024年4月でしたので、早くても2024年秋を想定していました。それが、1年も早い『MECT(メカトロテックジャパン2023)』へ出展するということになり、それからは怒濤のごとく、全体計画を調整し直し、各メンバーにも頑張ってもらいました」と寺川は言う。
「そういった経緯を聞き、私も気合いが入りました。一番苦心したのは、お客様にとってわかりやすいUIを探る作業ですね。当初は上から撮った写真だけを表示していたのですが、それではどこが最大ワークサイズを超えたのかがわかりにくいということで、3Dデータから側面図を作ってはどうかというアイデアが出ました。でも実際に側面図を作ってみると3Dデータのノイズが悪目立ちしてしまい、かえってわかりにくいということで没になりました。また、上から撮った写真にパレット位置での最大ワークサイズを丸で表示してみたのですが、写真はカメラより遠くのもの(背の低いワーク)は小さく、近くのもの(背の高いワーク)は大きく映るため、高さのあるワークは実際には最大ワークサイズを超えていなくても目印となる丸の大きさを超えてしまうという問題が生じました。結局、パレット位置での最大ワークサイズの丸と、最大ワーク高さの位置での最大ワークサイズの丸を2つ描くことで回避することにしました。ただ、自分としてはまだまだ完璧とはいえないため、今後も改良を続けていきます」と古田は語る。展示会出展のためのスケジュール前倒しという出来事は、それだけ社内での期待が高まっていたことを意味し、チームの団結力と意気込みを一層高めるきっかけにもなったのだ。
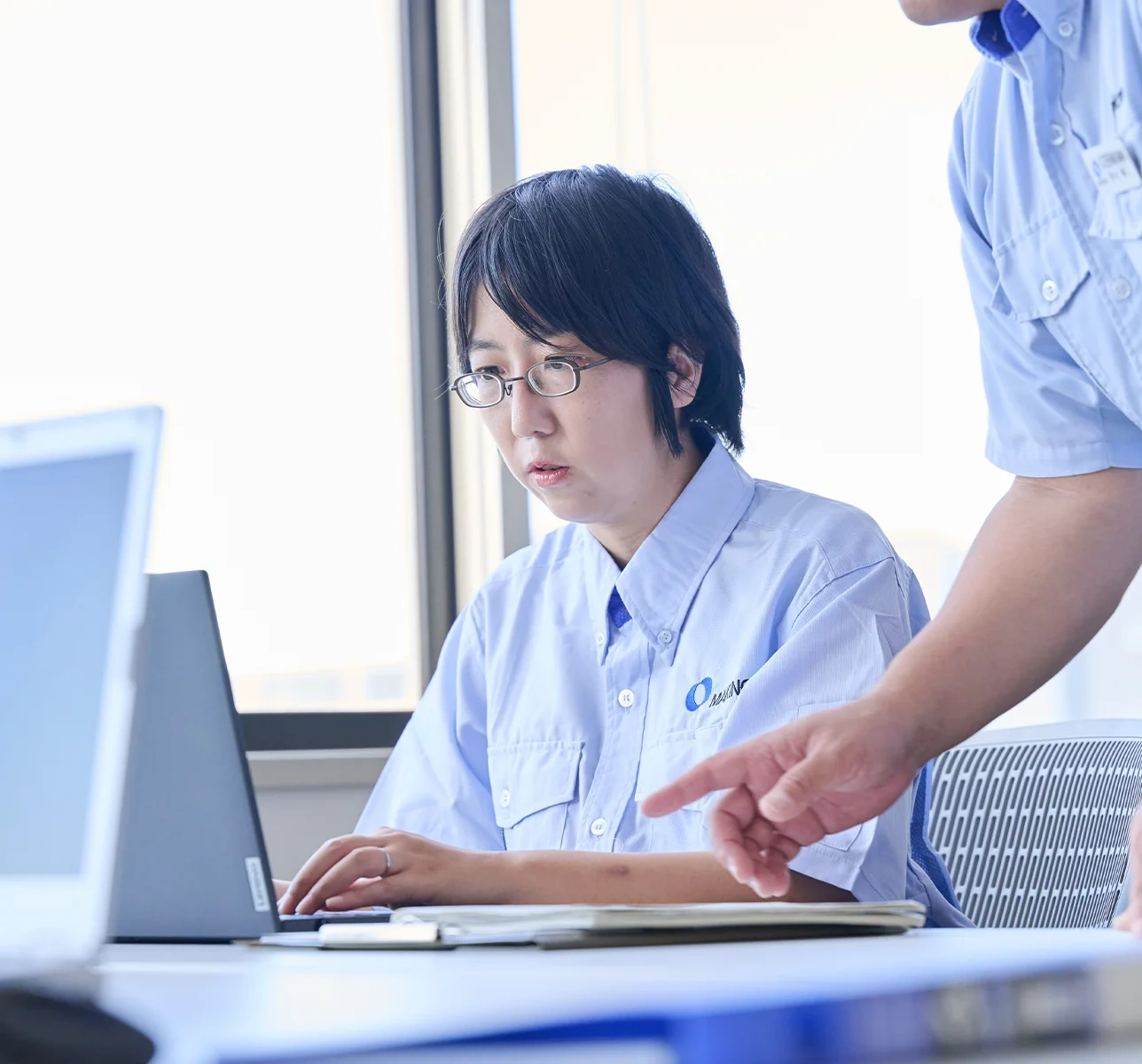
展示会での評判は上々。
勝因は、諦めずに全社で取り組む
“マキノイズム”
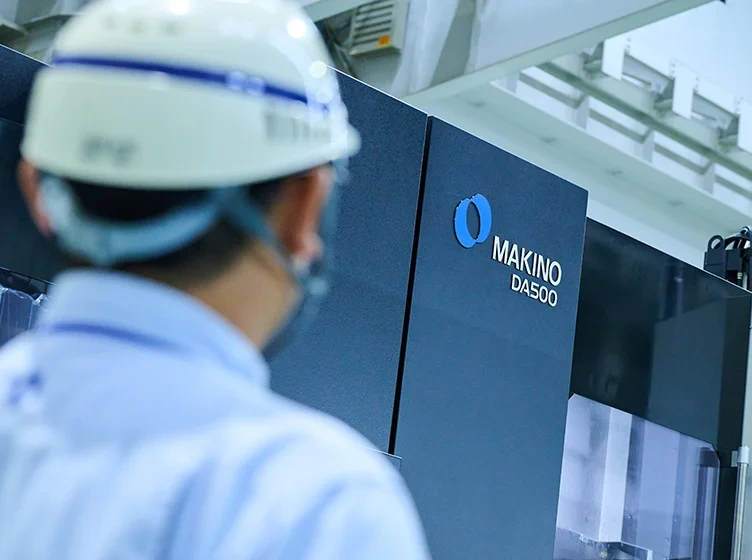
「展示会には、メンバーたちの奮闘のおかげでなんとか間に合わせることができました。お客様の反応もよく、社内の営業からも期待の声が聞かれました。本当に技術者一人ひとりの努力の賜物です」と寺川。たとえばここに登場していないが、メカ設計を担当したあるエンジニアは、機械のベースとなり高い静的精度が求められる部分の設計において、要求性能を満たしつつ、製造グループや出荷グループと設計時から話し合い、組立や出荷のしやすさなど機械トータルとしての最適化にこだわってくれたという。「海外出荷のしやすさも意識して、輸送寸法制限に工具マガジンも含めた機械全体の寸法が何とか収まるように調整してくれました。彼が言うには『マキノの先輩方は設計の知識や技量も、開発にかける熱量もやっぱりすごい。皆がよりよくしようと意見を出し合えるところがいい』と。『自分もメカ設計としてさらに成長し、自分がしてもらったように後輩を支えつつ、マキノの機械の進化に貢献したい』と思ってくれているようです。頼もしいですよね」と寺川は微笑む。
制御ハード担当の工藤は今回のプロジェクトを振り返り、「機械が進化し続ける限り“完成”という概念はありませんが、展示会への出展を一つの到達点としていたのでひと安心しました。改めて、機種開発というのは社内外の多くの人の協力と努力により成されるものと痛感しました。これから納入する多くのお客様に長く使い続けていただけるよう、今後も開発に励みます」と力を込める。
技術者たちは一様に、目標を達成できたのは多くの協力とマキノらしさ があったからだと口を揃える。旋削テーブルの開発を担当した矢口は、自身の設計ミスで部品が取りつかないというアクシデントがあったことを例に挙げる。「どうしようと困っていると、加工部門の方がすぐに手直ししてくれて、次の日には正しい形に仕上げてくれました。ありがたい、の一言でした」。こうした経験から、周りの皆が味方なのだという想いを強くしたという。
主軸を担当した石丸は「DA500では高速仕様と高トルク仕様の2種類の主軸を選択できるように開発したのですが、どちらの主軸も旋削機能を付けることができ、そのうえで切削加工性能も高水準です。この開発期間、一人として『多少切削性能を落としてもいいのでは?』『限られた条件でだけ使える仕様にしては?』といった消極的な意見を出す人はいませんでした。関係者みんなが実現のために知恵と技術を出し合って常に今より優れた工作機械の実現を目指す、マキノの社員らしいところだと感じます。これからも多くの人に支えられながら、そして自分も多くの人の支えとなれる技術者になりたいです」と結んでくれた。
切削加工と旋削加工のどちらも高いレベルで行える複合加工機能を備えた「DA500」の誕生。マキノはこれを皮切りにさらなる進化を目指していく。2023年10月に発売された「DA500」の歴史はまだはじまったばかりだが、さまざまな視点からの改良やお客様ごとのカスタマイズをいとわないマキノの開発者たちは、すでにこの先の展開を見据え、準備を進めている。
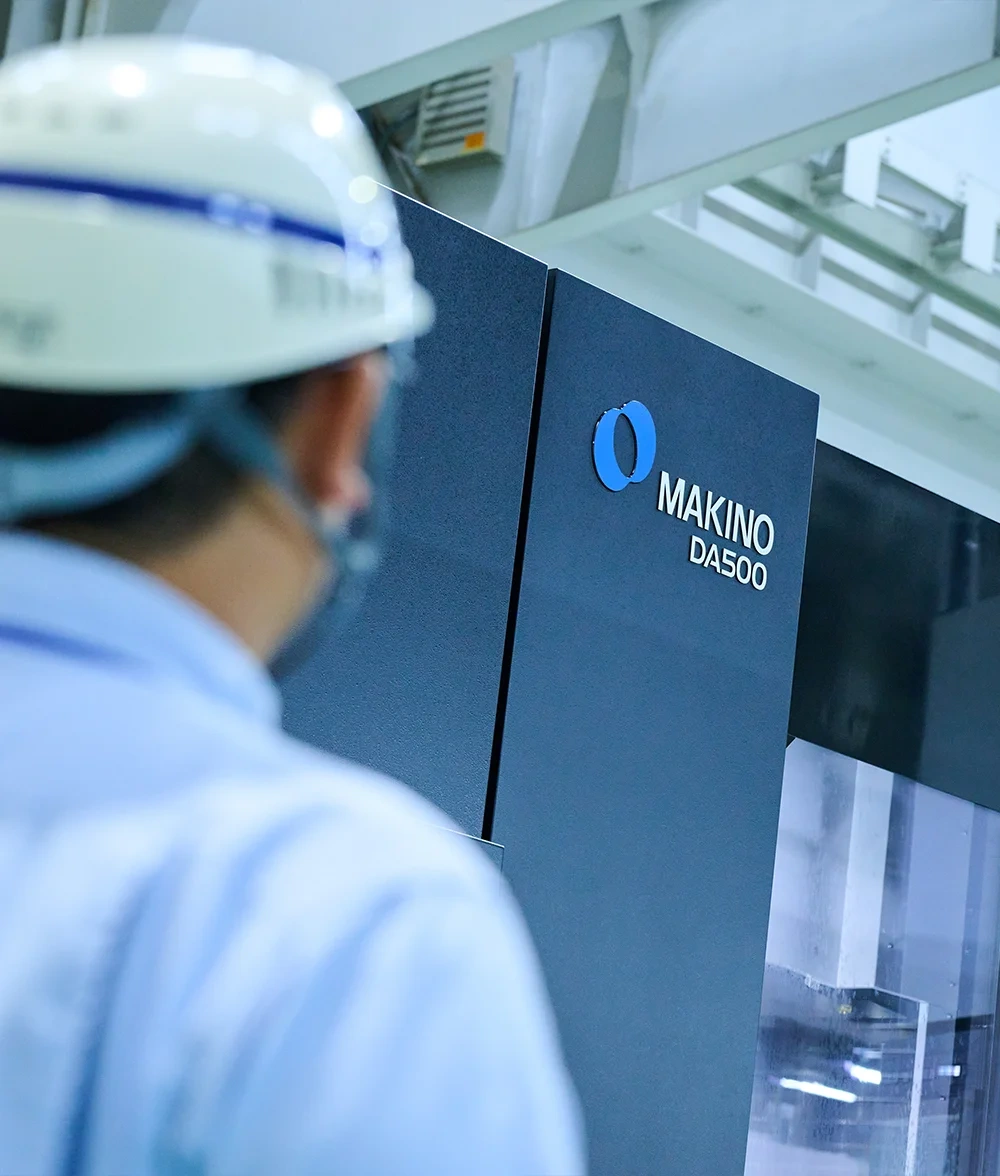
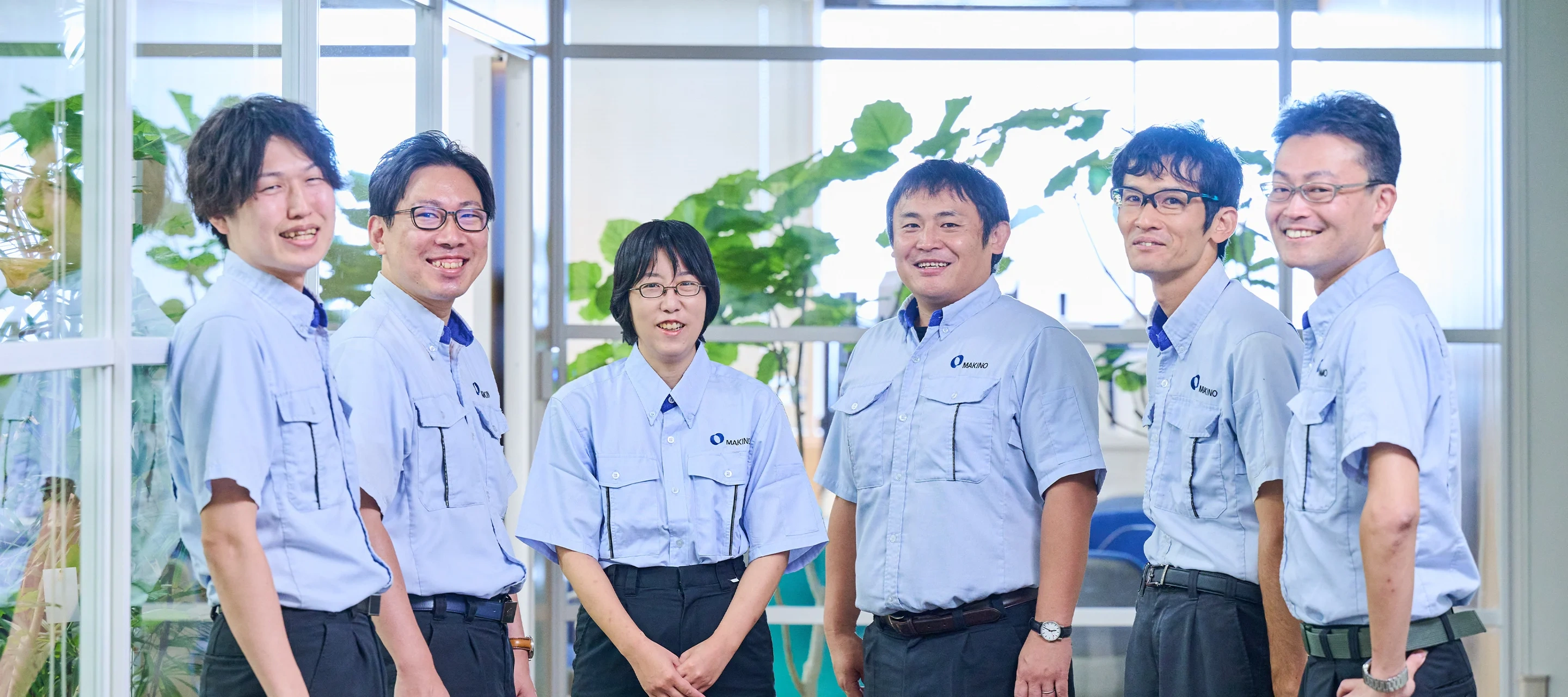
※掲載内容は、2024年10月時点での情報です。
NEXT STORY
ENTRY